Dynamiczne środowisko operacyjne oraz otoczenie rynkowe wymusza na firmach wprowadzanie efektywniejszych i wydajniejszych rozwiązań technicznych i organizacyjnych. Zgodnie z wynikami badań przeprowadzonych przez Autodesk, aż 71,6% badanych potwierdziło że wprowadzenie rozwiązań zakresu przemysłu 4.0 wpłynęło na wzrost ich przychodów. Najbardziej popularne są rozwiązania zakresu automatyzacji linii montażowych, jednocześnie nie można zapominać o procesach wspierających. Poprzez analogie jeżeli produkcję uznamy za serce sytemu to logistyka jest krwioobiegiem, który napędza jego funkcjonowanie. Nawet najlepsze serce nie będzie funkcjonowało poprawnie bez wydajnego krwiobiegu. Wyłącznie zrównoważony rozwój zapewnia spełnienie oczekiwań Klientów wewnętrznych i zewnętrznych.
Na przestrzeni ostatnich lat nastąpił dynamiczny wzrost rozwiązań automatyzujących realizację procesów logistycznych począwszy od obiegu informacji, a skończywszy na zarządzaniu materiałami. W BDO HBC Business Improvement łączymy ujęcie procesowe wraz z dostępnymi rozwiązaniami technicznymi, wyniku czego analizujemy i optymalizujemy procesy logistyczne w pięciu wymiarach:
- Efektywność & Wydajność – to obszar odpowiedzialny za zapewnienie właściwej oceny realizowanych procesów logistycznych, zarówno manualnych jak i maszynowych. Rozwój cyfryzacji zapewnia możliwość wdrożenia rozwiązań zautomatyzowanych oraz odpornych na błędy ludzkie. Dzięki czemu uzyskujemy wysoką szczegółowość uzyskiwanych danych przy minimalizacja zaangażowania pracy ludzkiej. W zakresie oceny wykorzystania parku maszynowego dostępnych jest bardzo wiele rozwiązań technicznych monitorujących ich wykorzystanie w sposób pośredni (z minimalnym zaangażowanie pracy ludzkiej) lub bezpośredni (bez angażowania pracy ludzkiej). W przypadku pracy manualnej możemy polecić system WPS (ang. Work Performance System), zapewniający cyfrowe monitorowanie efektywności pracy.
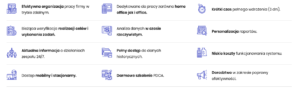
Rysunek 1 Cechy charakterystyczne systemu Work Performance System
Łatwość implementacji oraz elastyczność rozwiązania zapewnia możliwość efektywnego monitorowania realizowanych czynności logistycznych wraz z ich podziałem na VA, SVA oraz NVA. Obszar efektywności i wydajności jest pierwszym, który weryfikujemy ze względu na jeszcze jeden ważny aspekt. Podjęcie decyzji o automatyzacji jakiegokolwiek obszaru musi zostać poprzedzone analizą procesową oraz techniczną, a w obydwóch przypadkach wymagane jest oparcie się o rzetelne dane. Niestety historia licznych organizacji przedstawia, że brak właściwej analizy oraz oceny inwestycji jest „popularny” wśród Polskich organizacji.
- Identyfikacja materiałów – obejmuje rozwiązania umożliwiające identyfikację materiałów, od najbardziej popularnych kodów kreskowych 1D, poprzez kody 2D, a skończywszy na wykorzystaniu technologii radiowej RFID (ang. Radio-Frequency Identification). Połączenie kodów kreskowych 1D lub 2D wraz z automatycznymi skanerami pozwala na uzyskiwanie informacji o ruchu i/lub stanie danego procesu w sposób automatyczny. Aktualnie wiele firm oferuje w przystępnej cenie urządzenia wraz z bazami danych zapewniające automatyzację odczytu kodów kreskowych. Jednak wciąż to rozwiązanie jest obarczone jednym ważnym ograniczeniem, a mianowicie wymagane jest zapewnienie dostępu do kodu kresowego. W tym przypadku rozwiązaniem jest wykorzystanie technologii RFID, umożliwiającej „bezdotykowy” odczyt danych. Koszty implementacji RFID stają się coraz niższe, ze względu na niższe ceny tagów/znaczników (w głównej mierze pasowanych charakteryzujących się mniejszymi możliwościami technicznymi, niż ma to miejsce dla tagów aktywnych).
- Monitorowanie ruchu materiałowego – to przede wszystkim rozwiązania systemowe klasy WMS, wspierające realizację procesów logistycznych oraz systemy wspomagające pracę ludzką. Dostępne na rynku systemy WMS pozwalają m.in. na dynamiczne zarządzanie lokalizacją składowanych materiałów oraz pełną integracje procesów logistycznych i planistycznych. Systemy wspomagające prace ludzką są ukierunkowane na zapewnieniu idei poka yoke tj. zapobieganiu popełnienie nieumyślnych błędów przez operatora. Do głównych rozwiązań w tym zakresie możemy zaliczyć systemy pick/put to light, pick to voice oraz inne systemy kontrolno-pomiarowe.
- Obieg dokumentacji – nieodzowna cześć procesów logistycznych, która dzięki aktualnym rozwiązaniom może być realizowana w sposób elektroniczny. Od najbardziej zaawansowanych rozwiązań wymiany danych jakim jest EDI (ang. Electronic Data Interchange), który jednak wymaga wdrożenia po obu stronach procesu. W przypadku występowania tradycyjnych dokumentów efektywne może okazać się zastosowania rozwiązań OCR (ang. Optical Character Recognition), umożliwiających konwersję pliku graficznego (skanu dokumentu) do wersji cyfrowej. Dostępne algorytmy obliczeniowe oraz rozwiązania zakresu sztucznych sieci neuronowych pozwalają na uzyskiwanie wysokiej jakości i poprawności odczytywanych informacji i ich automatyczne wprowadzanie do systemów powiązanych (np. CRM, ERP).
- Logistyka wewnętrzna – to aktualnie jeden z najbardziej dynamicznie rozwijających się obszarów, do którego zaliczamy wykorzystywane modele transportowe oraz środki transportu. Aktualnie możemy wyróżnić dwa główne typy środków transportowych tj. AGV (ang. Automated guided Vehicle) oraz AMR (ang. Autonomous Mobile Robots). AGV to automatyczne wózki jezdne, które poruszają się po odgórnie zdefiniowanych trasach. Jak sama nazwa wskazuje są automatyczne, jednak nie autonomiczne. W tym miejscu pojawiają się wózki AMR, które są autonomicznymi mobilnymi robotami. Do głównych ograniczeń zarówno dla wózków AGV, jak i AMR możem zaliczyć konieczność pracy wewnątrz budynków. Oczywiście pojawiają się rozwiązania poruszające się po zewnątrz, niedawno takie rozwiązanie zostało uruchomione w firmie Seata w Martorell (jednak jest to odmienny klimat od uwarunkowań panujących w Polsce). W przypadku rynku krajowego można zaobserwować liczny wzrost rozwiązań z zakresu AGV oraz AMR, jednak o ograniczonej ładowności (wynoszącej maksymalnie około 0,5 tony dla AMR i 1 tony dla AGV). Firmy transportujące cięższe ładunki muszą poszukiwać rozwiązań na rynku zagranicznym, w śród takich dostawców rozwiązań technicznych jak Dematic czy Proxaut. Połączenie automatycznych/autonomicznych wózków wraz z urządzeniami peryferyjnymi tj. automatycznymi stacjami załadowczymi oraz wyładowczymi pozwala na zbudowanie efektywnego i wydajnego systemu transportu wewnątrz zakładowego. Równocześnie na rynku pojawiają się automatyczne/autonomiczne zestawy logistyczne, które mogą pracować w pętlach logistycznych. Przykładem jest firma AutoGuide, która oferuje autonomiczne holowniki mogąc ciągnąć tradycyjny zestaw logistyczny – obejmuje rozwiązania zakresu przechowywania materiałów, ale również automatycznego wyładunku/załadunku środków transportowych. W tym obszarze możemy wymienić m.in. bardzo popularne regały windowe, jak również w pełni zautomatyzowane, wielkopowierzchniowe systemy magazynowe takich producentów jak m.in. Remmert czy Matter. Wsparte automatyzacją załadunku i/lub wyładunku środków transportowych zapewniają wysoką wydajność i efektywność.
Gama rozwiązań zakresu automatyzacji i optymalizacji procesów logistycznych jest bardzo szeroka. Jednak należy pamiętać, iż podstawę dla całej automatyzacji stanowi właściwie zdefiniowany proces. Bezwzględnie pierwszym krokiem przy podjęciu decyzji o automatyzacji jest przeprowadzenie mapowania procesów, aby poznać aktualne uwarunkowania oraz uwzględnić je w przyszłym modelu funkcjonalnym. Stan przyszły podlegający wdrożeniu winien zapewniać osiągnięcie efektu synergii z zastosowania poszczególnych rozwiązań technicznych oraz współpracy na styku człowiek-maszyna.
Należy podkreślić, iż automatyzacja jest wyłącznie jednym z elementów przemysłu 4.0, który posiada jeszcze wiele innych ciekawych elementów do zaoferowania. Osoby zainteresowane tematyka automatyzacji procesów logistycznych zapraszamy do dołączenia do grupy „Automatyzacja procesów logistycznych” w serwisie LinkedIn oraz na stronę www.hbc.pl.